
Dusty trails
The Glitch:
Take a look at the vent connector piping shown in Figures 1a, 1b and 1c. These photos were all taken at pellet boiler installations. Do you see something in common? What’s the issue and what can be done to resolve it?
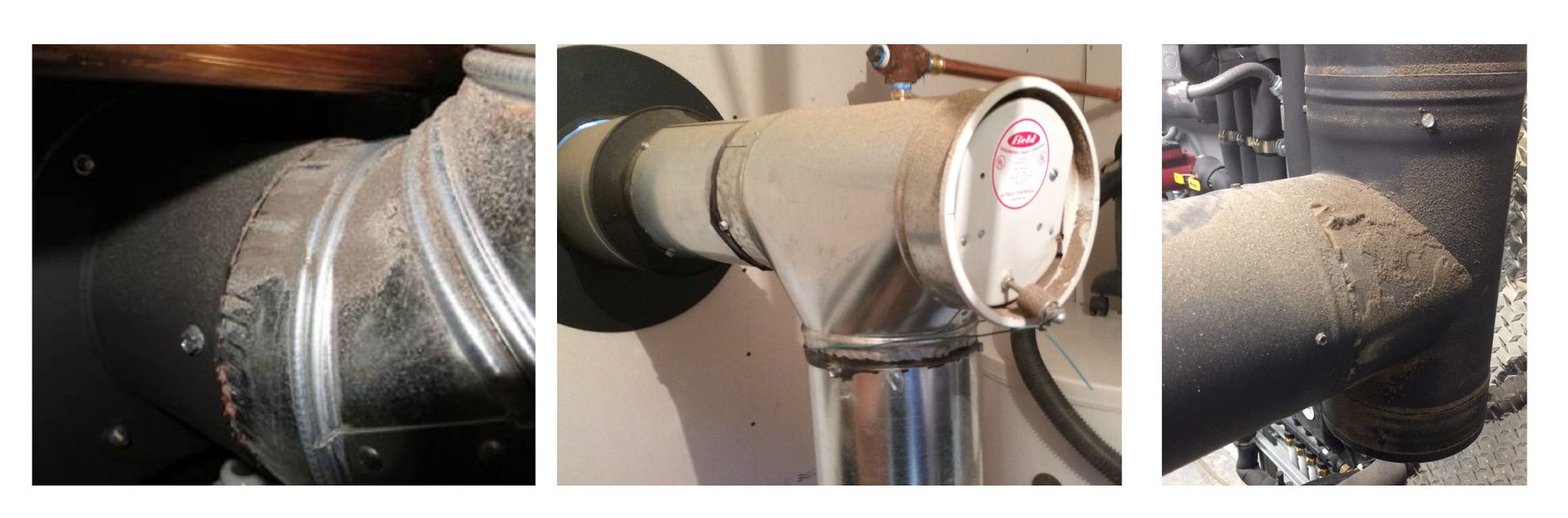
ENLARGE
FIGURE 1
Modern pellet-fueled boilers are sophisticated devices. Most of them have an internal draft-inducing blower. The speed of that blower is regulated based on the oxygen content of the flue gases. This allows the boiler to adjust the excess air supplied to the combustion chamber to maintain optimal combustion efficiency.
Properly configured pellet boiler systems incorporate thermal storage, and should only require the boiler to fire for 2 to 3 times on a typical winter day. This implies that there will be several hours when no flue gases are passing up the chimney. The chimney will cool off during those times.
In situations where a modern pellet-fired boiler is combined with a “cold” chimney, the flue gas flow created by the boiler’s inducer blower at startup can be higher than the initial drafting ability of the chimney. The result is slight positive pressure in the vent connector piping. The flue gases and any small amount of fly ash present in the exhaust stream will find any exit point in the vent connector piping assembly. That’s why you see the ash accumulating on the outside of the vent connector joints and draft regulator in Figure 1. This condition is especially problematic with an exterior masonry chimney due to its high thermal mass. Following a cold start on a winter day, that type of chimney can take a while to establish a good draft.
Are you an ace troubleshooter?
Within the pages of this magazine, PM’s Hydronics Editor John Siegenthaler, P.E., will pose a question to you, our readers, to review a system’s schematic layout and discover its faults, flaws and defects. Discover archived “The Glitch & The Fix” exercises at its radiant-focused website, www.radiantandhydronics.com. Good luck!