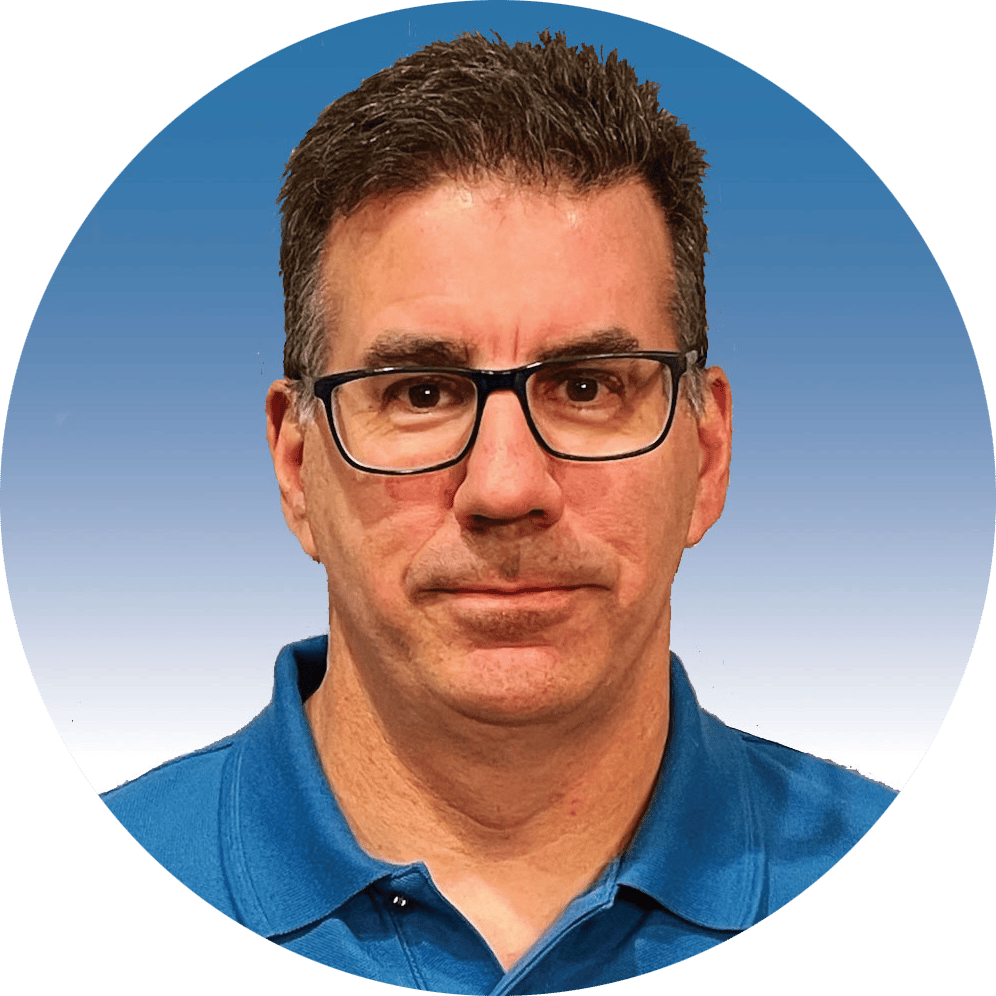
HEATING PERCEPTIONS
BY Scott Secor
MANAGING YOUR BUSINESS
Hidden issues and high bills: troubleshooting radiant heat in a luxury home
A seven-figure renovation leaves a high-end radiant heating system underperforming.
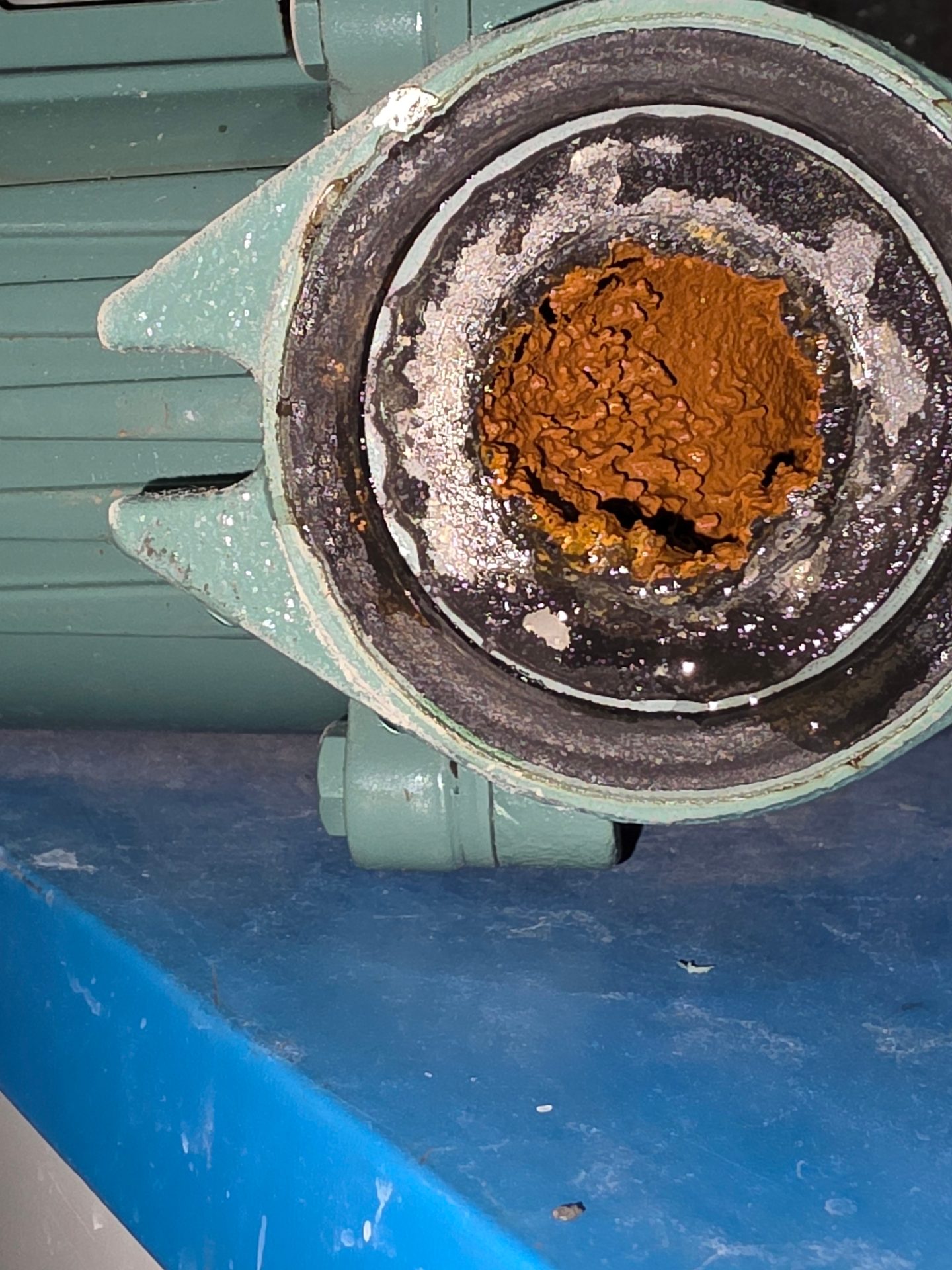
Due to the buildup inside the two iron pumps, we suggested adding a magnetic separator and chemical cleaner to the system. Image Courtesy of Scott Secor
Recently, we were asked by a plumber to look at a home that has issues with the radiant heat. Turns out the homeowner (we will call him Ronny), runs a company that builds commercial office buildings, and the plumber that recommended us does the plumbing work.
On my first visit to the house, I was greeted by the housekeeper. She did not speak English and was unaware that Ronny, the homeowner, had made the appointment. I called Ronny and spoke to him; he apologized for forgetting the appointment. He stayed on the phone as I walked though his 7000 square feet house, and explained the heating issues to me while pointing out all eighteen radiant manifold locations, the boiler room and many of the thermostats. For about 30 minutes, I felt like a doctor that does telehealth. Once we ended the phone call, I spent about an hour in the boiler room taking photos, taking notes, and trying to figure out why the entire radiant system was not producing heat.

The radiant heat was producing almost no heat in the entire home. Image Courtesy of Scott Secor
The two Slant Fin Sentinel gas fired atmospheric cast iron boilers provide the heat and feed the two eighty-gallon indirect hot water tanks. The boiler room piping was almost all copper. The piping all appeared to be correctly sized. There were a total of four single speed cast iron circulator pumps, which also appeared to be sized about right. In the boiler room, there were a total of fourteen zone valves, and three more remote zone valves. There were numerous Tekmar remote thermostats with Tekmar relays that connected to the pumps and boilers. Both boilers were vented into a masonry chimney, and fresh air was piped into the mechanical room ductwork from outside.
Ronny purchased the home from an older gentleman that had the house built. The original owner founded a familiar retail chain that was (and still is) quite successful. Soon after Ronny purchased the home, he decided to update almost everything: new windows, a large addition, new roof, siding, tile floors, eight or nine bathrooms, etc.
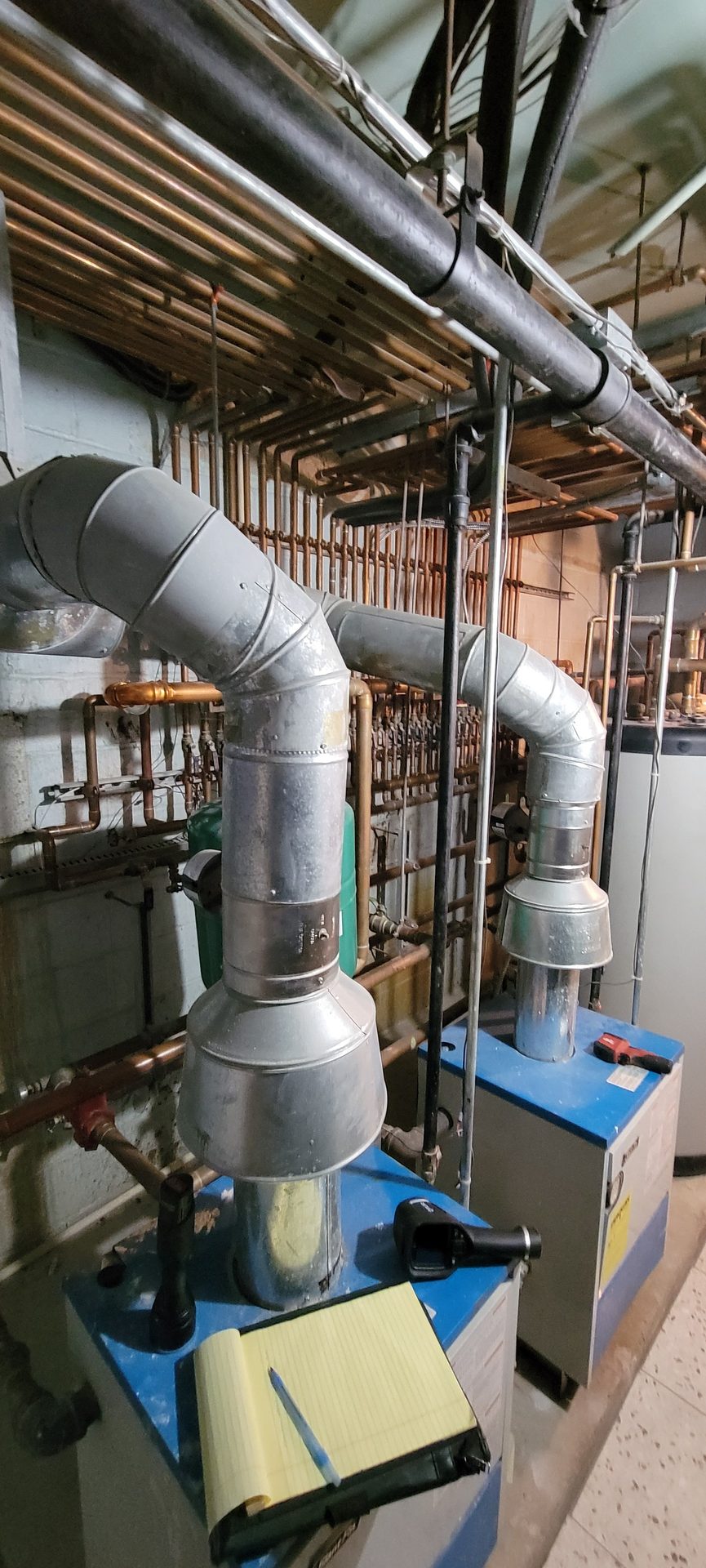
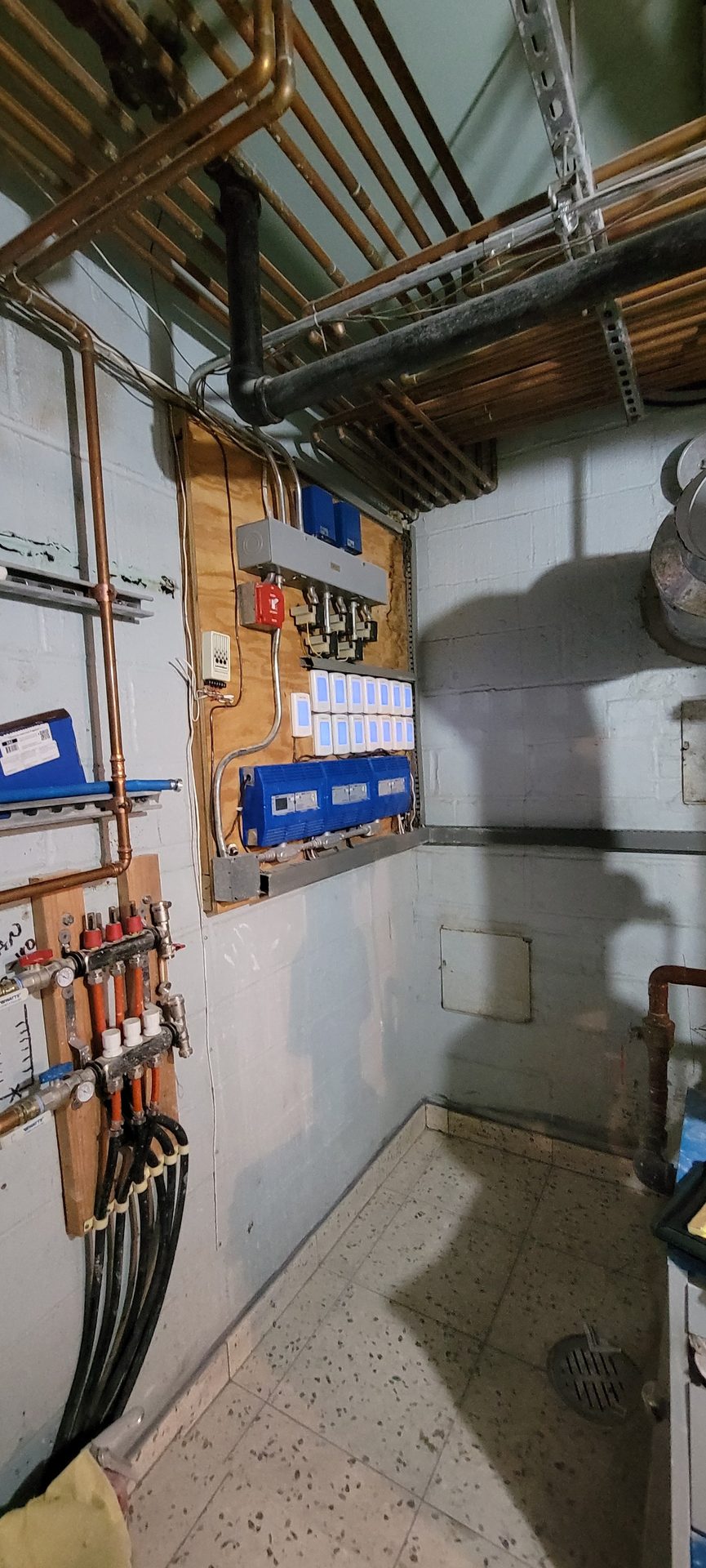
The two Slant Fin Sentinel gas fired atmospheric cast iron boilers provide the heat and feed the two eighty-gallon indirect hot water tanks. Image Courtesy of Scott Secor
When I was speaking with Ronny, I learned that the home had central air conditioning with electric heat as a backup. This past winter, the heating (electric) bills were over four thousand dollars per month. I gathered that the radiant heat was producing almost no heat in the entire home, and they were forced to use the electric heat. I noticed that one of the original Taco circulator pumps was installed incorrectly, and another pump was making noise like it was time for a replacement. The original radiant tubing appeared to be the black rubber type, Entran Onix. He claimed that the house heated perfectly when the construction took place, but mentioned that he had all the radiant manifolds replaced soon after he purchased the home. He said the heat has not worked since the manifolds were replaced.
We proposed to replace the two pumps that needed attention, inspect the pipe internals, test each stat and zone valve, shoot every radiant heated floor of the house with our infrared cameras, and go over the rest of the system with a fine-tooth comb. As part of the proposal, we would also provide a drawing of the heating system. Ronny agreed and asked us to start ASAP.
The home had central air conditioning with electric heat as a backup. This past winter, the heating (electric) bills were $4000 per month. I gathered that the radiant heat was producing almost no heat in the entire home, and they were forced to use the electric heat.
When we arrived, we started in the boiler room and permed the work we proposed. Remarkably, the boiler fire side and the breaching was spotless. The two suspect pumps were loaded with deposits and the nearby piping had a light coating. We found two bad zone valves in the boiler room. Every thermostat worked perfectly as did the control panels. Due to the buildup inside the two iron pumps, we suggested adding a magnetic separator and chemical cleaner to the system. We also suggested replacing the two zone valve heads; Ronny agreed and asked us to proceed with the work.
We suspect oxygen was getting into the system. When we flushed the system one zone at a time, it certainly helped: we saw a lot of rusty water coming out of our garden hose. We also suspected that the two pumps we replaced were not flowing enough water to be effective. The two zone valves that failed deliver the heat to the master bedroom and master bathroom.
Once the work was completed, we took our shoes off and took readings in every area of the home. Every floor was heating when the thermostat was calling for heat. Ronny was happy, and wrote us a check on the spot for the work that was completed. We plan on returning next week to flush out the cleaner, clean the magnet again, and add the conditioner to the system. Over the summer, we will likely inspect the interior of the boilers and the two other circulator pumps, because I am concerned that these items may also be comprised.
Scott Secor runs a small heating business in New Jersey. Founded by his father, Ken Secor, in 1976, Scott began working for the business in the summer of 1986 while attending college. In 2006, he purchased the business and has been running it ever since. The company designs, installs and services steam and hot water heating systems. Contact him at scottsecor@comcast.net.