Hydronic pressurization unit helps maintain Chicago-area assisted living facility
CASE STUDY
Hydronic pressurization unit helps maintain Chicago-area assisted living facility
CASE STUDY
Mikrofill 3 helps 235-unit retirement community identify potential costly leaks.
An altogether new way to maintain hydronic system pressure, the new Mikrofill 3 is helping the 235-unit Marian Village retirement community identify potentially costly leaks in its four-pipe boiler/chiller system before they can cause major problems and costs.
An altogether new way to maintain hydronic system pressure, the new Mikrofill 3 is helping the 235-unit Marian Village retirement community identify potentially costly leaks in its four-pipe boiler/chiller system before they can cause major problems and costs.
Mikrofill 3 helps 235-unit retirement community identify potential costly leaks.
BY JOHN O'REILLY
The very first installation of the Mikrofill 3 hydronic pressurization unit in North America took place recently in a mechanical room of an assisted- and independent-living community in Southwest-suburban Chicago. You might say the flower of this innovation grew from the soil of an old industry friendship.
A 45-year HVAC industry veteran, Local 597 retired pipefitter Ed Dory and manufacturers representative Tom Buchanan have worked with one another for more than a decade. Their relationship dates back to when Dory served as a service manager for a local mechanical contracting company that Buchanan’s agency, AIM Solutions (Downers Grove, Illinois), regularly serviced on large commercial HVAC projects.
When Buchanan recently came across new technology — wholly unique, in fact, for the U.S. market — for maintaining water pressure and volume in hot- and chilled-water HVAC systems without any need for a pump or a backflow preventer, he immediately thought of his savvy, long-time customer as the perfect candidate to lead the debut.
The retired Dory currently consults on plumbing and mechanical systems at Marian Village, an independent living and assisted living community, one of several operated by the Franciscan Sisters of Chicago. Located an hour’s drive southwest of downtown, Marian Village was constructed in the early 2000s. It consists of 72 coach homes, 27 rooms for assisted living and 136 apartments for independent residents.
The main structure is divided into three large segments with the South Building and the central Assisted Living Units (ALU) served by a single HVAC and domestic hot water system, which Dory assists in monitoring and working with maintenance manager Vince Tam and his three-person crew.
The system’s core is a rooftop chiller, made by Carrier; and, in the basement mechanical room, a pair of gas-fired, Bryan commercial boilers with a total input of 1.5 million Btu/h. It’s a closed, four-pipe system — supply and return for both hot and cold water — that operates 24/7/365.
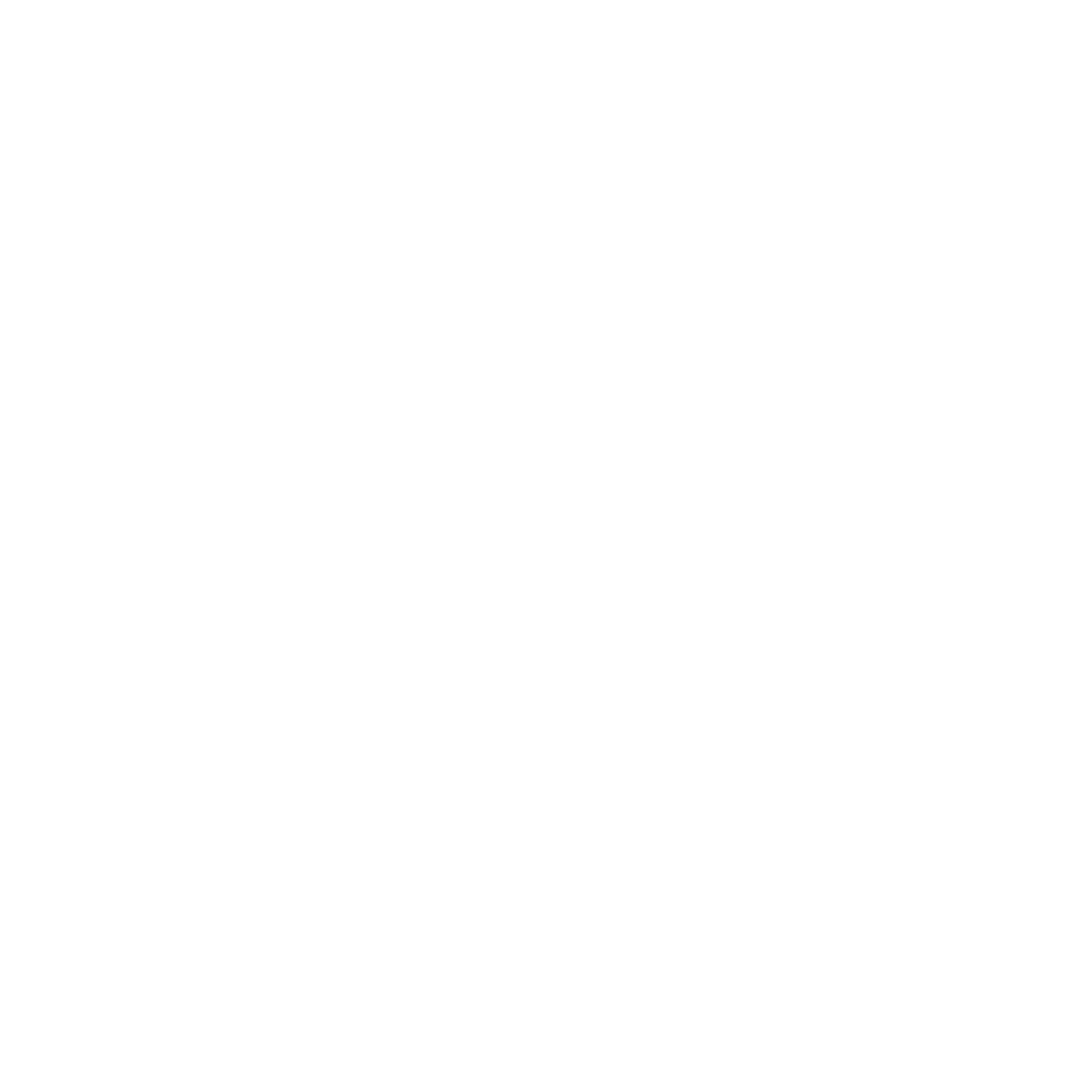
Proven effective in the United Kingdom for more than two decades, the Mikrofill 3 is a “direct-type” pressurization unit intended specifically for sealed, low-pressure hot-water and chilled-water applications, like the one at Marian Village.
Heat is piped to the ALU and delivered via baseboard radiation on the walls. The South Building receives its climate control through an air handler and reheat coils in the ductwork running to the apartments.
“We typically pump 55° F air through the ducts,” explains Dory. “The coils inside the ducts then adjust the air temperature to whatever level the residents desire in their rooms.”
Another key system component is a heat exchanger, also situated in the basement mechanical room, providing residents with domestic hot water. This equipment was installed 22 years ago.
“The boiler’s running all the time, 12 months a year, so why not install a heat exchanger to generate DHW year-round as well?” Dory says.
All this machinery is original equipment for the Marian Village, and the system performs very well, as it absolutely must for a senior population that cannot afford to be without heating, air conditioning and hot running water for very long — if at all. Actually, the critical nature of those ongoing needs was one of the big reasons Buchanan introduced Dory to the Mikrofill 3.
“If the Mikrofill 3 can be trusted in a critical facility like this,” says Buchanan, “you can certainly trust it in a more conventional boiler application.”
System leaks: No small problem
A mechanical system like the one at Marian Village must inevitably cope with the issue of water leaks, which will reduce pressure in the boilers and serve as a drag on overall comfort and performance. Historically, the maintenance team has depended on their own vigilance to uncover these leaks, as well as the problems they can create for the entire system — and beyond.
Dory recalls a day not long ago when he decided — by chance, just before heading home — to check on the North Building boiler, a separate system that had been having “issues,” he recalls.
“I open the mechanical room door, only to see water pouring from the top of the pump” and flooding the room.”
If not for Dory’s fortunately timed inspection, the flood waters of the leaking system, situated at the top of the four-story structure, might well have cascaded down through the entire building to the first floor, causing catastrophic damage.
The Mikrofill 3 is engineered to help facility managers avert that type of close call. Proven effective in the United Kingdom for more than two decades, the Mikrofill 3 is a “direct-type” pressurization unit intended specifically for sealed, low-pressure hot-water and chilled-water applications, like the one at Marian Village. Able to fill any heating or chilled water system from empty without the use of a pump, the product also delivers commercial backflow protection with no RPZ valves.
But the leak and flood protection derives from the Mikrofill 3 continuously monitoring system inlet and operating pressures through a series of pre-commissioned sensors that automatically maintain system presets. By recognizing a change in cold-fill water pressure, these sensors open the Mikrofill 3 valves to top off the system, stopping the fill once the required pressure has been reached.
But what if that pressure is not reached due to a system leak?
- Small leaks will prompt continuous topping off the boiler or chiller. Once a preset number of refills has been reached (25 refills over a 24-hour period is typical; 50 is the maximum), the integral color-screen display on the top-front side of the Mikrofill 3 will indicate a problem;
- Larger leaks may, in fact, prevent proper replenishment. If the Mikrofill 3 does not detect the expected pressure increase over a preset period, the unit will shut down to prevent further water damage; and
- In the case of catastrophic leaks, the Mikrofill 3 will quickly close off the main water supply to prevent further damage.
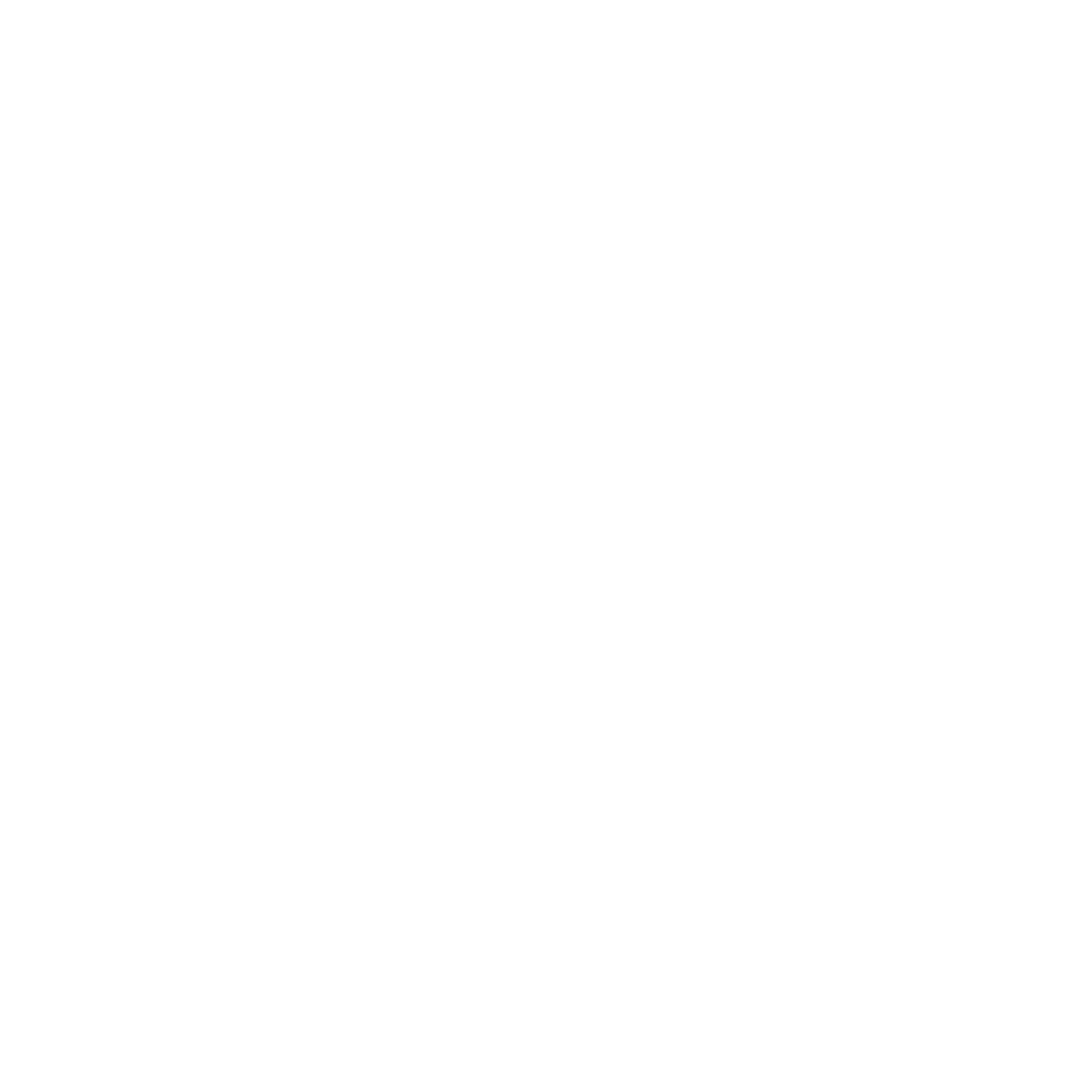
Able to fill any heating or chilled water system from empty without the use of a pump, the Mikrofill 3 also delivers commercial backflow protection with no RPZ valves.
Peace of mind
Dory quickly warmed to Buchanan’s offer to make the Mikrofill 3 an integral part of the Bryan boiler system. For one, Dory liked the idea of eliminating the pressure-reducing valve that had been used to maintain incoming water pressure from the municipality.
“The PRVs we use are spring-type valves that adjust by turning a screw on top,” he says. “The problem is, they are not as accurate as digital controls, which are the future of this business.”
Dory also welcomed eliminating the system’s old backflow preventer. “No more backflow preventer means the facility saves money by avoiding the cost of the required annual inspections.”
Most of all, he likes the peace of mind that Mikrofill’s system monitoring delivers by preventing a leak situation from getting badly out of hand: “The old-fashioned feeder system doesn’t pump much water, but it also never stops,” says Dory, explaining the fill process of the boiler system at Marian Village.
“If a leak starts after everyone in maintenance has gone home, the PRV will continue to feed the boiler through the night, which means the leaking will continue too. The PRV may sense a pressure drop, but that drop will just trigger the valve to keep feeding. It will have no clue there's a problem.”
Meanwhile, as the leak continues, all the attending costs are amplified, notes Dory. “The cost of the wasted boiler water, the cost of all the chemicals used to treat that water, and the cost of repairs and recovery from the flooding — it all goes up and up as time passes.”
The day of the installation of the Mikrofill 3, Buchanan was ready to actively assist. But that proved unnecessary. Installer Rich Friedman, vice president of service at Zentel Tech (Joliet, IL), had no serious problems connecting the unit, finishing in just “a few hours,” says Dory.
“The device is very simple: Two water lines, one in and one out, drainage and power. Not much to it,” he continues. “All Rich had to do was cut out the backflow preventer and the PRV, hook the water lines to the Mikrofill unit and hang the device on the wall. Fortunately, we had a 120-volt box hanging close by, right where we had planned to mount the device.”
Other than substituting a U.S. flex connector for a similar U.K. component shipped with the unit whose diameter didn’t fit into the Marian Village’s system, no other issues slowed Friedman’s successful completion of the install.
New mentality
Beyond obtaining the necessary permissions from Marian Village management, Dory had no misgivings over the Mikrofill 3 technology and its newness to the American market. By way of explanation, he points to the ongoing, routine incidence of European innovation in hydronics: “New stuff comes from Europe all the time these days.”
Indeed, Dory and Marian Village are already planning their second installation of a Mikrofill 3, this time on the ALU’s rooftop chiller system, keeping it topped off with a 30% glycol solution for outdoor freeze protection. A break tank connected to the system stores and releases the glycol solution whenever system pressure drops below a preset level. Once installed, the Mikrofill 3 will be monitoring and managing that process, just as it currently does with the two boilers in the mechanical room four levels below.
To date, the latter system has continued to perform well, according to Dory. But it has taken a bit of time and a new mentality to fully appreciate the Mikrofill 3 and its essential role in a hydronic heating system.
Dory recalls a recent problem with a relief valve on one of the boilers, which led the new Mikrofill device to stop filling the system. “It sensed a leak somewhere. So, we found it and fixed it.”
But shortly after, the maintenance crew discovered yet another leak, this time in a grooved fitting. Once again the Mikrofill would not permit filling the boiler. The initial reaction was…frustration. The new device was somehow causing problems — “messing us up,” says Dory, by not allowing the system to be filled.
“So, I had to explain: Hey, the controller won’t let us fill the system because we have leaks. The controller is not the problem. It’s doing what it's supposed to do, telling us we have leaks that we must fix.
“It’s doing its job — and that’s a good thing!”

Photos courtesy of Greenhouse Digital + PR.
John O’Reilly is principal and account leader at GreenHouse Digital + PR, an independent communications agency, specializing in digital marketing, social media and public relations solutions for professionals in the design and construction industry. Based in suburban Chicago, O’Reilly can be reached at john@greenhousedigitalpr.com.